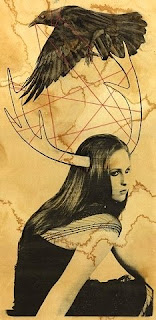
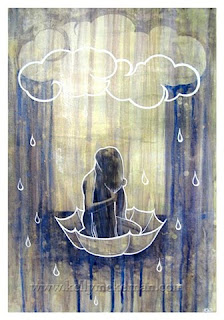
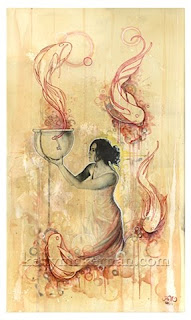
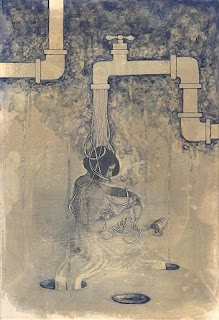
BLACK MAGIC is probably the most comprehensive product system of its kind and thus offers advantageous features:
• high speed/high silver content thus delivering short exposure times even with large format pictures and exceptionally high maximum density
• a complete modular system with interchangeable components
• 3 different emulsions, two graded and one variable contrast emulsion
• RBM23 excel by high edge sharpness and have a cold image tone due to its silver bromide halides
• RBM33 features variable contrast control and has a neutral image tone due to its chlorobromide silver halides
• long shelf life and exceptional archival qualities due to adding a minimum quantity (0,1%) of a powerful fungicide and bactericide (phenol) for long term conservation
• BLACK MAGIC additive RBM52 is free of formaldehyde and chromium potassium sulfate due to a new formula and acts as a powerful hardener
• The whole product system is backed up by proven high quality photographic chemistry which will deliver excellent results
ROLLEI BLACK MAGIC delivery assortment:
1. Safety first
In all areas of life, any product may be harmful if not used properly. Of course this applies also to photographic products.
We at MACO care about our customers and our responsibility in regard of environmental aspects.
Therefore we have kept any potential health hazards to a minimum. However we urge you to use appropriate caution in handling our photographic products.
• Always keep the products out of the reach of children !
• Please read the instructions carefully - if in doubt please contact us for support.
• Working with photographic chemistry should take place in rooms with good ventilation.
• Furthermore, we keep Material safety data sheets available.
2. Usage
The use of BLACK MAGIC should take place in a black & white darkroom.
The graded BLACK MAGIC emulsions RBM23 may be mixed together in any ratio.
3. What do you need - a checklist
Depending on your goal, you should have all necessary components at hand. If you miss an important tool or material during your work it is too late. Most items are ready available in a well equipped darkroom - but some are special and have to be organised before your coating session:
Checklist:
1. First you have to decide what type of material you want to coat (see chapter 8 for detailed information).
2. Check the contrast of the negatives you want to use - do you have different grades, then go for BLACK MAGIC VC emulsion RBM33, or do you have fairly consistent contrast negatives, then go for BLACK MAGIC hard RBM23.
3. For most coating applications the method of brushing will prove to be the best - get yourself a wide brush (5-10 cms/ 2"-4" width) made of natural hair, e.g. a Japan brush.
4. Keep small measures for quantities of 20- 50cc at hand, it will be useful for adding small amounts of RBM52.
5. For coating metal, plastic, glass or ceramic tiles, a precoat with alkyd resin primer or oil-based polyurethane paint should be carried out, these special primers are available at art shops.
6. If you have absorbent materials such as textile fabric, papers or wood it is recommendable to precoat these materials with BLACK MAGIC pure photographic gelatin RBM41.
7. For liquification, you will need a bucket to be filled with warm water (40-45°C / 100 - 115 F).
8. If you want to liquify just a small amount, you need BLACK MAGIC special bottle RBM60.
9. For keeping a bigger amount liquified in order to coat large areas or several objects, it is best to fill the liquified emulsion into a smaller bucket (plastic or stainless steel or enamel coated only only) and place this bucket into a larger container filled with warm water to keep the emulsion liquified.)
10. For improving mechanical resistance you need BLACK MAGIC ADDITIV HD RBM52.
11. In order to make coating easy and keep the problem of unwanted bubbles low you need spirit (grain alcohol).
412. Check your safelight before coating, in order to avoid unwanted fogging (see chapter 7 for details).
13. If you want to store materials coated with light-sensitive emulsion, have enough lighttight containers at hand, the containers should be designed in a way that these will cope with the wet emulsion (high moisture).
4. How much area can be coated
With non-absorbent materials, you can coat up to 8 m2, with absorbent materials you can coat up to 4 m2.
In practical use, this may vary due to the thickness of the coating and the absorbent properties of the chosen material.
5. How do you store BLACK MAGIC
The liquid emulsions RBM23 and RBM33 should be stored in the refrigerator (6°C-8°C / 40 - 46 F).
All other components, RBM41, RBM52 and RBM60 can be stored at room temperature.
6. How long is the shelf life
If stored according to our instructions, shelf life will be one year. If you deep freeze RBM23 and
RBM33 at temperatures below -10 C° / 14 F shelf life will be extended by far.
7. What type of Safelight is suitable
RBM23: red or yellow green RBM33: red or light brown, no yellow green
Keep in mind, that silver halides collect light in difference to the human eye.
Therefore, it is advisable to keep safelight exposure to a minimum. In reality no safelight is really safe - it's just a matter of exposure time. We recommend to do a fogging test under your own conditions - this is especially important if you want to coat large areas or many objects.
Carry out a trial coating and let it be exposed partially by your safelight at the place you want to coat all other materials. Place a black cardboard on top and move it in a way that you have an exposure bracketing of 15 minutes/ 30 minutes/ 45 minutes and so on.
Develop and see whether any exposure shows a gray fogging. If this is the case move or change your safelight.
8. What different approach is recommended for each type of material to be coated
Depending on the chosen material, the thoroughness of your preparation will be decisive for your final art work.
All materials have to be free from dust and grease. If in doubt clean twice - any trace of grease will lead to adhesion problems.
After you have selected a material to be coated, there is a different approach for 3 main groups of materials:
1. Absorbent materials such as fabric, papers or wood; if you want to prevent the emulsion to be soaked into the base, a precoat with BLACK MAGIC RBM52 - pure photo gelatine has to be made (also called baryta solution, but without barium sulphate).*
2. Smooth and/or hard materials like polished stone, glass or metal: we recommend a pre-coating with RBM41. It is also possible to skip this step and start directly to work with the liquid emulsion. Should you note that the emulsion is coming off during handling, try to use the following tips, maybe you will come to terms with them perfectly:
1. Mix our pure photo gelatine with distilled water (Barytage dissolution). Coat the glass board with it. Let the gelatine become touch dry. Does not have to hard-dry. Afterwards, you rinse the gelatine coating with hot water. Don’t use any cloth, sponges or the fingers! Only rinsing under hot water, nothing else. After drying the class is perfectly prepared and ready for the coating with Black Magic.
2. If there is still a watery dissolution creeping at the rim under the coating in spite of this preparation, then you have to find a way to avoid this. It is possible. You just have to coat the rim of the glass board that is completely coated with Black Magic with a 1-component grout sealing agent e.g. from a sanitary dealer.
4. All other materials can be coated directly with BLACK MAGIC photographic emulsion. With 3-D objects several thin coats ensure high maximum density (after setting before complete drying).
5. How to make a baryta solution: (this step may be carried out under normal lighting conditions)
Warm up 1000cc tab water until 70°-80°C and dissolv e completely 40 grms of RBM41 by continuous stirring, until free of lumps. To reduce surface tension you may add a few drops of ROLLEI WETTING AGENT (wetting agent with bactericide and fungicide additives) to your solution, this makes it easier to evenly coat smooth /hard materials. Coat your material directly afterwards. To improve hardening of the emulsion add 20 - 50 cc of BLACK MAGIC additive RBM52 to your solution. Since you coat under normal lighting conditions even coating will be much easier.
6. Note about hardening: You can harden indirectly by adding BLACK MAGIC additive RBM52 to the baryta solution and harden directly by adding BLACK MAGIC additive RBM52 to the light sensitive photographic emulsion (in this case, please use the photographic emulsion within 2 hours). For better adhesion of the coating and to improve mechanical resistance of the surface you may combine both methods.
Furthermore, you can add BLACK MAGIC additive RBM52 directly to the developer.
9. How do you combine the modular components of the BLACK MAGIC system
The graded BLACK MAGIC emulsion RBM23 may be mixed together in any ratio, to achieve in between grades. For a wide range of contrast control use BLACK MAGIC RBM33.
For absorbent materials use BLACK MAGIC RBM41, it is a purified photo gelatin, much cleaner than gelatin for food, and add for improved mechanical resistance BLACK MAGIC ADDITIV HD RBM52 instructions at the end of this manual, due to its special formula you can add RBM52 also to the emulsion itself and to the developer.
It's much easier to warm up partial amounts of emulsion if you use RBM60, the special bottle is lighttight and thus you avoid warming up the complete bottle - spare time and keep the emulsion quality high.
6
Spirit (grain alcohol) is recomended in order to get rid of bubbles which almost always occur. Add 10- 20cc of it directly into the liquified emulsion (amount based on 500cc). If you have a longer coating session, you can add spirit (grain alcohol) every 20 minutes.
10. How to achieve different image tones
If you decide to precoat your material with BLACK MAGIC RBM41, you can add water soluble photographic dyes to the solution - add as much until you have the desired tone, usually a few drops will suffice.
11. How does the liquification take place
Take out BLACK MAGIC photographic emulsion of your refrigerator and...
Carry out following working steps under safelight conditions !
Either take out the needed amount out of the bottle by using a solid plastic or stainless steel spoon fill it into the special bottle (article RBM60) and liquify it up in a bucket filled with warm water (35-40°C).
For larger application projects warm up the original bottle by the same means.
1. To change or water down the consistency of the light-sensitive coat, please do not stirr distilled water into the Black Magic! This would change sustainably the adhesive strength characteristics in a negative way. You better mix a Barytage dissolution with pure Black Magic photo gelatine. In this case only the silver content is reduced and the coating is perfectly suitable to make several applications.
Note:
For first trial coatings or smaller objects to be coated just take out needed amounts (under darkroom safelight) out of the original bottle , put them into a graduate and liquify by warming up in a container (or bucket) filled with warm water. By doing so you will ensure the quality of BLACK MAGIC (repeated warming and cooling harms light sensitive products).
If you want to coat larger objects (e.g. ceramics, stones) you may heat them in your oven (30-40°C /86 - 104F) so your emulsion won't set while you are still coating.
12. What are the different ways of coating
If you have never worked with BLACK MAGIC photographic emulsion before, you can train the coating procedure with coffee cream since this liquid has a similar viscosity.
You can coat your objects different ways:
*Use only spray guns with large jet opening, an air brush is not suitable.Wear protective clothing/mask to avoid inhaling spray particles.
For most applications best results will be achieved by using a brush with natural hair (e.g. Japan brush).
We recommend to coat test stripes at the same time for determining the correct exposure later on. Preferably of the same material or the backside of photographic paper).
Excessive emulsion may be reused immediately.
Note:
By using an spray gun, you can adjust viscosity with distilled water up to an ratio of 1:1. By doing so spray several layers.
Setting stage:
Cooling and setting stage follows directly after coating. In this stage the coated surface is very delicate. Setting will take about 1 to 2 hours. You can speed up setting by storing the coated materials in the refrigerator for about 30 min. To avoid unwanted exposure either use a light-tight container or unscrew the bulb of your refrigerator.
Drying stage:
Now you can dry the coated materials. You can do so by using a hair dryer at low heat setting and midrange distance to avoid melting of the emulsion. Check hair dryer by turning it on in the dark before using it to make sure there is no electrical spark or glowing of the heat wires which could cause an exposure. Of course you can store objects in your darkroom (Do not turn on room light!) and let them dry off. This will take between several hours and 1 day depending on the kind of object and humidity.
13. Exposure - what do you have to consider
Procedure is similar to standard photographic paper, especially if you have coated flat materials. With 3-dimensional objects close down your enlarging lens to the maximum to reach maximum depth of field. (Note that by stopping down your lens, depth of field will be 1/3 before and 2/3 behind point of focus)
Hint: With cylindrical or evenly formed objects you can produce a large halftone negative(or if you wishalso a graphic negative without grey values)
pour and pan
=
with flat and rigid materials such as tiles, metal plates etc.
pour and brush
=
with almost all materials
dip and dunk
=
with smaller 3-dimensional objects
spray*
=
with large and complex structured objects
7
by using GENIUS Litho Film. This negative can then be laid or taped onto your coated object (e.g. a bottle or a vase) and then turn it evenly under the enlarging light - by doing so a sharp and even exposure will be a lot easier !
Note:
If you have used LPE310 for coating, you can change grades for optimum photographic results. This can be done equivalent to standard variable contrast photographic papers (e.g.ROLLEI Vintage 111 etc.) either with filters for your filter drawer (e.g. LABOR PARTNER Fil 8, ORIENTAL Acrylicfilter,or ILFORD Multigrade Filter) or with enlargers with Variocontrast - or Colorhead by turning the corresponding filter values:
Yellow = for softer image reproduction
Magenta = for harder image reproduction
Note:
In case you exposure was to intense, you can bleach until desired density is reached by using ROLLEI RST SEPIA PART A, Art. No. RST52, dilution 1+30.
14. Processing - what is important for good results
Due to the high silver content, use high energy photographic chemistry only.
ROLLEI photochemistry is especially well suited for BLACK MAGIC. Keep working temperature to a max. of 20°C or lower, to avoid damaging of the emulsion.
Developer: Rollei RPN, for universal application Rollei RHC, for steeper grade
Short rinse: Rinse with tab water or dunk in water filled tray to for 10-20 seconds
Stopbath: Rollei CITRIN, odorless, non allergic and environmentally friendly
Fixer: Rollei RXA, pH-neutral for non acidic fixing, improved archival quality, avoids sulphur dioxide emissions, shorter washing times
Washing: tab water, 68 F / 20°C, duration depending on coati ng thickness and base material.
Wetting agent: Rollei RWA, 3rd generation, with bactericide and fungicide additives
After treatment: Rollei SELENIA, unsurpassed quality for protection of image silver, improved image brilliance
Drying: Air drying, in case of need use a hair dryer